Knowledge database
MIG vs. TIG vs. Handheld Laser Welding: When UK Manufacturers Should Make the Switch
The UK manufacturing landscape is experiencing a welding revolution. While MIG and TIG welding have served British industry well for decades, handheld laser welding is emerging as a disruptive technology that offers compelling advantages for specific applications. This article examines when laser welding makes financial and operational sense for UK manufacturers currently using traditional methods.
Understanding the Three Technologies
MIG (Metal Inert Gas) Welding uses a continuously fed consumable wire electrode and is generally faster and easier to learn than TIG. It excels with thicker materials and offers high production rates.
TIG (Tungsten Inert Gas) Welding employs a non-consumable tungsten electrode and provides superior precision and control. It produces cleaner, more aesthetically pleasing welds but operates at slower speeds.
Handheld Laser Welding utilises a focused laser beam to create precise, high-quality joints with minimal heat input. This technology operates 5-10 times faster than conventional methods while producing minimal heat distortion.
Financial Analysis: Equipment Costs in the UK Market
Initial Investment Comparison
MIG Welding Equipment:
Entry-level models: £200-£1,000
Professional systems: £1,000-£5,000+
Industrial units: Up to £3,000+
TIG Welding Equipment:
DC TIG welders: £680-£910
AC/DC TIG systems: £840-£1,035
Professional models: £1,000-£2,000+
Handheld Laser Welding Systems:
Entry-level units: £10,000-£15,500
Professional systems: £15,000-£22,500
Safety enclosures*: £8,300-£12,800 additional
*If used in a separate room, an enclosure is not necessary.
Operating Cost Benefits
Energy Consumption
MIG welding typically draws 5–7 kW while active, with energy use averaging around 0.08–0.12 kWh per metre on 2 mm stainless steel. TIG is slightly lower in peak power (4–6 kW), but slower weld speeds often mean higher total energy use per metre. Handheld laser welding systems are significantly more efficient, drawing just 2–3 kW and consuming roughly 0.03–0.05 kWh per metre – often 60–70% less than MIG or TIG over the same job.
Labour Time
MIG offers fast deposition rates but usually requires extra time for post-weld cleanup due to spatter and distortion. TIG is the slowest of the three, with some jobs needing multiple passes, especially where precision is critical. Handheld laser welding excels in speed, producing clean, high-quality welds with little to no post-processing. In production environments with good fit-up, this can result in 30–50% labour savings compared to traditional methods.
Consumables & Rework
MIG welding involves ongoing costs for wire, tips, nozzles, and grinding disks, with spatter and heat distortion often requiring rework. TIG uses durable tungsten electrodes but still relies heavily on filler rods and shielding gas, and often needs oxide removal. Laser welding typically eliminates the need for filler on thin materials and produces minimal spatter or heat-affected distortion. As a result, scrap rates are lower and up to 40% less rework is needed, especially when weld appearance matters.
Training and Support Considerations
MIG and TIG welding are well-established, with a broad base of skilled workers, training courses, and off-the-shelf support. MIG is generally the quickest to learn and easiest to deploy, with consumables and spare parts widely available. TIG offers the highest level of manual control and precision, but it comes with a steeper learning curve and longer setup times – making it more suited to specialist applications or highly skilled teams.
Handheld laser welding introduces something different: while it requires upfront investment and some specific safety measures, the training curve is actually quite manageable. Most operators can reach production-level competency in just a day or two of hands-on use. Once safety procedures are in place, the process is fast, clean, and consistent – but it does rely on supplier support to get the most out of the technology.
At OptoWeld, we deliver that support directly. We don’t just drop off a machine and walk away – we train your team on-site, help you dial in parameters for your materials and processes, and stay available for ongoing technical support. From Class 4-compliant safety setups to real-world welding advice, we work closely with manufacturers to make sure their investment in laser welding delivers real, long-term value.
Sector Applications in UK Manufacturing
Automotive Manufacturing
MIG remains the workhorse for chassis rails, sub-frames and other thick-gauge steel parts where high deposition rate and gap-bridging matter more than cosmetics.
TIG shows up in prototype work and cosmetic joints on stainless exhausts or thin aluminium body panels, but its lower speed makes it rare on high-volume lines.
Handheld laser welding is carving out its space on EV battery modules and lightweight mixed-metal joints (e.g. aluminium-to-copper busbars). Body-in-white trials in the UK report up to 8× faster panel seams while still holding ±0.3 mm.
Aerospace Components
MIG is used mainly on thicker structural fixtures and ground-support tooling where weight isn’t critical.
TIG is still the benchmark for thin-walled titanium ducts and safety-critical welds – operators can nurse every millimetre, but travel speed is measured in millimetres per second.
Handheld laser welding is gaining share on hermetic fuel-system enclosures and thin Ti shells that can’t tolerate distortion. UK primes quote leak-rates below 1 × 10⁻⁹ mbar L s⁻¹ and stable joints at 1200 °C.
Medical Device Production
MIG rarely features – heat input and spatter are hard to reconcile with sterile environments.
TIG has long been the go-to for stainless surgical tools and cobalt-chrome implants; it can produce neat 0.5–1.0 mm beads but often needs post-polish and passivation.
Handheld laser welding now produces 0.2 mm, pore-free welds with almost no HAZ discolouration. Because the beam is non-contact, manufacturers meet ISO 13485 cleanliness targets without extra cleaning chemistry.
General Fabrication & Repair
MIG dominates job shops for frames, brackets and repairs on everything from trailers to farm gates – cheap wire, fast travel, tolerant of fit-up.
TIG steps in when the metal is thin, exotic, or the customer wants a “stack-of-dimes” finish.
Handheld laser welding is still new to many fabricators, but it’s already making a strong case in areas where precision, material conservation, and post-weld cleanup matter. Companies like Yorkshire-based Tadweld, supported by a Made Smarter grant, are using laser welding to repair small, heat-sensitive parts with minimal distortion and excellent joint quality. The focused beam means less filler is needed, less grinding and polishing afterwards, and cleaner finishes even on reflective or awkward geometries. For repair work in particular, laser welding can restore fine parts without compromising surrounding material – something MIG and TIG often struggle with.
When Handheld Laser Welding Makes Sense
Handheld laser welding proves most advantageous for UK manufacturers when:
Working with thin materials (under 6mm) requiring clean and precise
Joining dissimilar metals in EV or electronics applications
Speeding up welding and needing minimal post-weld processing to reduce labour costs
Operating in clean environments like medical device manufacturing
Requiring portable solutions for on-site repairs and fabrication
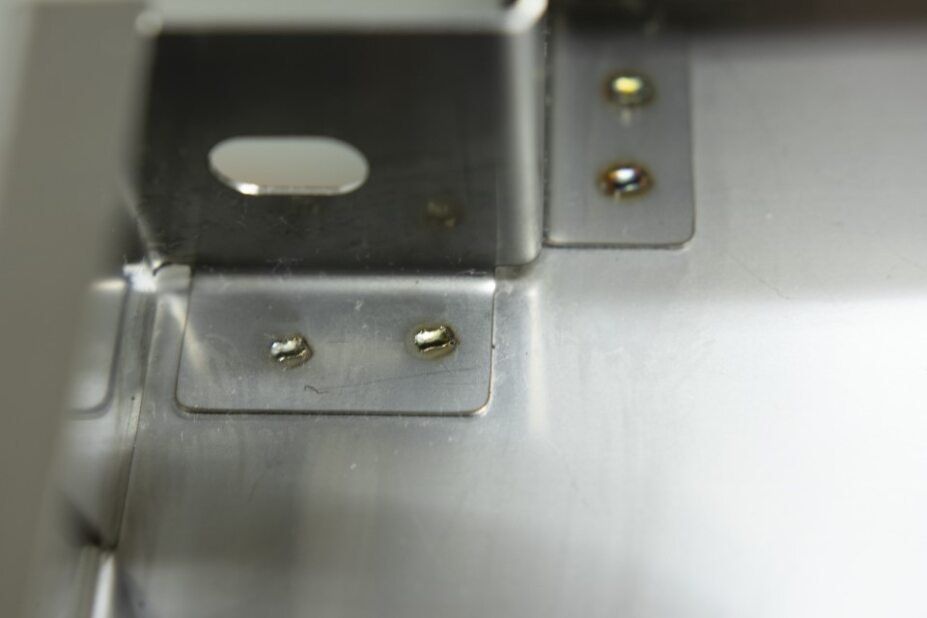
Conclusion
Handheld laser welding represents a significant opportunity for UK manufacturers seeking enhanced precision, speed, and cost-effectiveness . While initial investment exceeds traditional methods, operational savings and productivity gains deliver compelling returns for appropriate applications. The technology particularly suits manufacturers working with thin materials, requiring high precision, or operating in sectors like automotive, aerospace, and medical devices where quality standards are paramount.
The UK’s growing adoption of laser welding technology reflects its potential to maintain manufacturing competitiveness in global markets. For manufacturers currently using MIG or TIG welding in suitable applications, handheld laser welding offers a clear path to improved efficiency and reduced operational costs.
Laser welding is more accessible than ever. If you’re considering the switch, we’re here to help. Contact us at info@optowelduk.com