Dynamic Beam Shaping for High-Power Laser Beam Welding
Location: WMG, The University of Warwick, Coventry, UK
Date: January 28, 2025
Overview of the workshop
The workshop on Dynamic Beam Shaping for High-Power Laser Beam Welding held at the WMG, University of Warwick, showcased the latest developments in laser welding technology and its transformative potential for manufacturing industries. The workshop was chaired by Pasquale Franciosa from WMG, bringing together leading experts, the event highlighted innovative solutions, research insights, and applications that are reshaping the landscape of advanced manufacturing.
A key theme throughout the day was the rapidly evolving landscape of laser welding, driven by advancements in automation, digital manufacturing, and precision technologies. As industries such as automotive, aerospace, and energy seek more efficient solutions, laser welding is becoming a critical enabler for achieving high-quality, durable welds with minimal material waste.
Academic and industrial collaboration
Simon Webb from WMG set the stage by emphasizing how the High-Value Manufacturing (HVM) Catapult is accelerating innovation for UK industries. He stressed the importance of collaboration between academia and industry to translate research into tangible industrial impacts. This framework provided context for understanding the role of laser technology in maintaining the UK’s competitive edge.
Mark Thompson of Photonics Express presented an in-depth analysis of the UK laser welding market, which is projected to see significant growth driven by technological advancements and industry demand for precision manufacturing. Mark noted the increasing adoption of AI and IoT in welding processes, enabling real-time monitoring and predictive maintenance and highlighted the ongoing shift towards dynamic beam and fiber lasers, which are displacing traditional methods like MIG and TIG welding. Despite its relatively small market size, the UK’s leadership in laser research and development positions it as a key player in the global laser welding landscape.
What is Dynamic beam shaping?
Dynamic beam shaping allows for the adaption of laser parameters dynamically, ensuring optimal welding conditions for a wide range of materials and thicknesses. Ruben Cesana from CIVAN Lasers introduced the audience to this groundbreaking technology, which uses Coherent Beam Combining (CBC) and Optical Phased Arrays (OPA) to precisely control beam shape and distribution.
Machine learning enhances development
Volkher Onuseit of IFSW delved into the potential of combining dynamic beam shaping strategies with machine learning. By manipulating capillary dynamics and leveraging Bayesian optimization, researchers have developed ways to reduce defects such as spatter and transverse cracks. This approach minimizes the costly trial-and-error traditionally associated with fine-tuning welding processes, accelerating the path to optimal manufacturing outcomes.
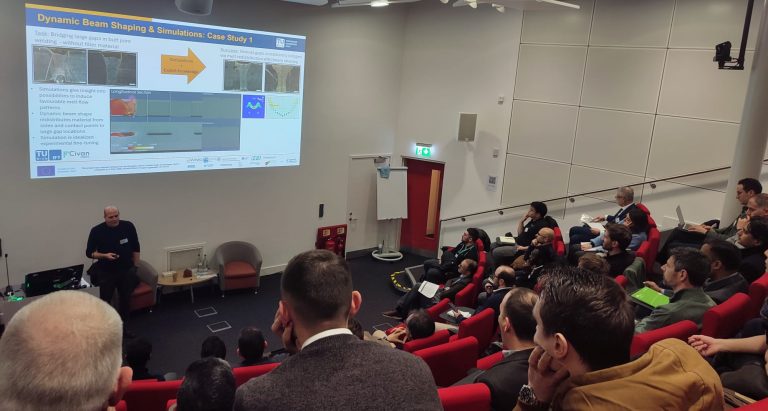
The applications of dynamic beam shaping
Through case studies on welding aluminum and copper alloys Aleksey Kovalevsky from the Israel Institute of Metals, demonstrated how dynamic beam shaping has enabled defect-free, high-speed welding without the need for filler materials. This technology is essential for industries that demand lightweight and strong materials, such as automotive and aerospace sectors.
Simone Peli from Castellini took the audience deeper, literally, into the capabilities of dynamic beam shaping. He shared insights into achieving weld depths up to 45 mm in a single pass, a feat that dramatically reduces material handling and production times. By overcoming challenges such as solidification cracks through multi-pass strategies, Castellini’s approach exemplified how advanced laser welding can revolutionize heavy industry applications, including shipbuilding and renewable energy infrastructure.
Domenico Stocchi of ECOR International presented the development of a digital “shadow” (or twin) for TIG manual welding processes. This platform captures and analyzes key parameters, enabling real-time monitoring and quality assurance. The potential to digitally track and optimize welding operations aligns perfectly with the Industry 4.0 vision of smarter, more efficient manufacturing.
Summary of Technological Insights
Dynamic beam shaping enables manufacturers to produce a wide variety of high-quality welds consistently and efficiently, by allowing precise control over thermal gradients, melt pool stabilization, and weld geometry.
One of the most remarkable achievements highlighted at the workshop was the ability to achieve welds up to 45 mm deep. Additionally, dynamic beam shaping was shown to be invaluable in applications involving copper and aluminum welding, including EV battery cases and compressed copper cables.
OptoWeld in the Wild
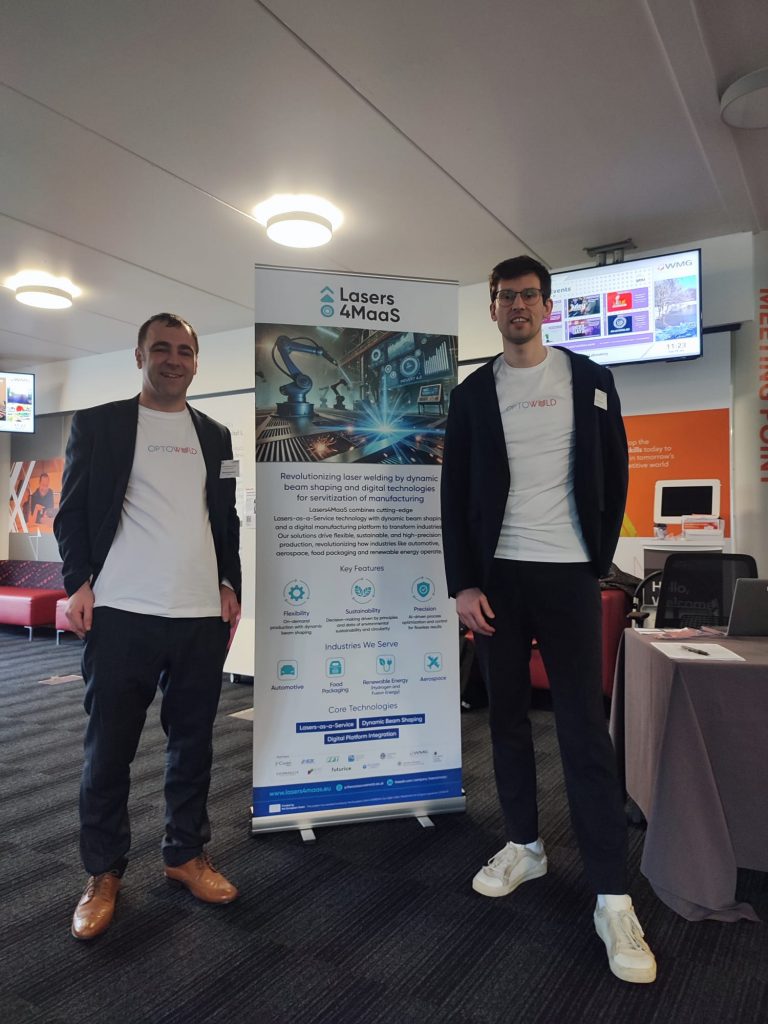
This event was a valuable opportunity for us to gain insights, engage with industry leaders, and explore innovative solutions that can benefit laser welding in the UK.
We look forward to continuing conversations, forming new partnerships, and contributing to the development of cutting-edge welding technologies. Stay connected with us for updates on how we’re driving innovation forward!