Knowledge database
What Metals Can you Weld with Lasers?
Laser welding has become an essential technology in modern manufacturing, offering high precision and efficiency across a wide range of materials. This technology enables the welding of various metals with minimal heat-affected zones, providing unmatched control over weld quality.
To achieve optimal results with laser welding, factors such as surface preparation, joint design, filler wire use, welding parameters, and the use of inert gas are critical. These elements play a significant role in ensuring strong, durable welds. For a more in-depth discussion on these aspects, read more here.
In this article, we will explore the compatibility of laser welding with different types of metals. The metals covered include::
- Carbon Steel: Various grades known for their strength and versatility.
- Alloy Steel: Includes commonly used alloy steels with enhanced properties.
- Stainless Steel: Various grades with a focus on corrosion resistance and mechanical strength.
- Tool Steel: High-hardness steels used for manufacturing molds and dies.
- Aluminium: Commonly used alloys with unique welding challenges.
- Titanium: High-performance alloys valued for their strength and corrosion resistance.
Each section delves into specific grades and their characteristics, detailing how laser welding can be applied to achieve optimal results. By understanding the properties and welding requirements of these metals, manufacturers can leverage laser welding technology to enhance product quality and operational efficiency.
Carbon steel
Carbon steel, known for its strength and versatility, is widely used in construction and manufacturing. Laser welding enhances these qualities by providing high precision and strong joints across various grades of carbon steel.
To achieve optimal results, it’s important to consider preheating and post-weld heat treatment, especially for medium and high carbon steels.
Low Carbon Steel (e.g., A36, 1018)
These steels are highly weldable due to their low carbon content. Laser welding offers clean, strong welds with minimal risk of cracking.
Typically, preheating is not necessary for low carbon steels, but it can be beneficial in preventing potential issues in thicker sections or during complex welding operations.
Medium Carbon Steel (e.g., 1045)
Medium carbon steels require careful control of heat input to prevent cracking. Laser welding’s precision ensures high-quality welds while maintaining the material’s mechanical properties.
Preheating is often necessary to reduce the risk of thermal stress and cracking, and post-weld heat treatment is recommended to restore the material’s toughness and relieve residual stresses.
High Carbon Steel (e.g., 1095)
High carbon steels are prone to cracking due to their hardness. Laser welding minimizes heat input and allows for controlled cooling, resulting in strong, durable joints.
Preheating is essential for high carbon steels to prevent rapid cooling, which can lead to brittle welds. Additionally, post-weld heat treatment is crucial to temper the steel, reduce hardness, and improve the overall ductility of the weld.
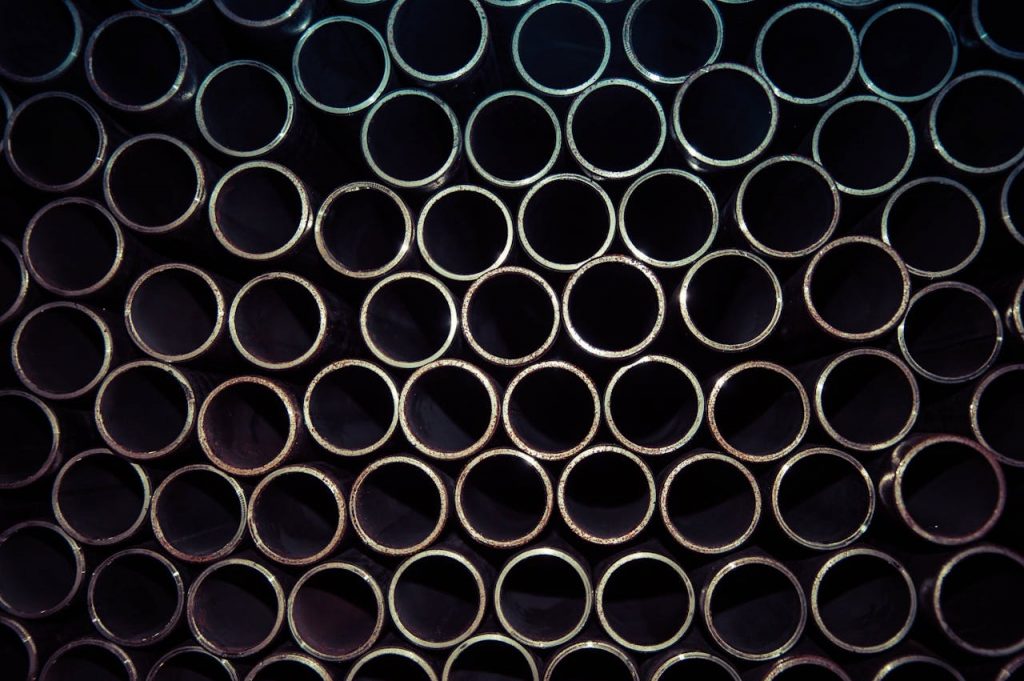
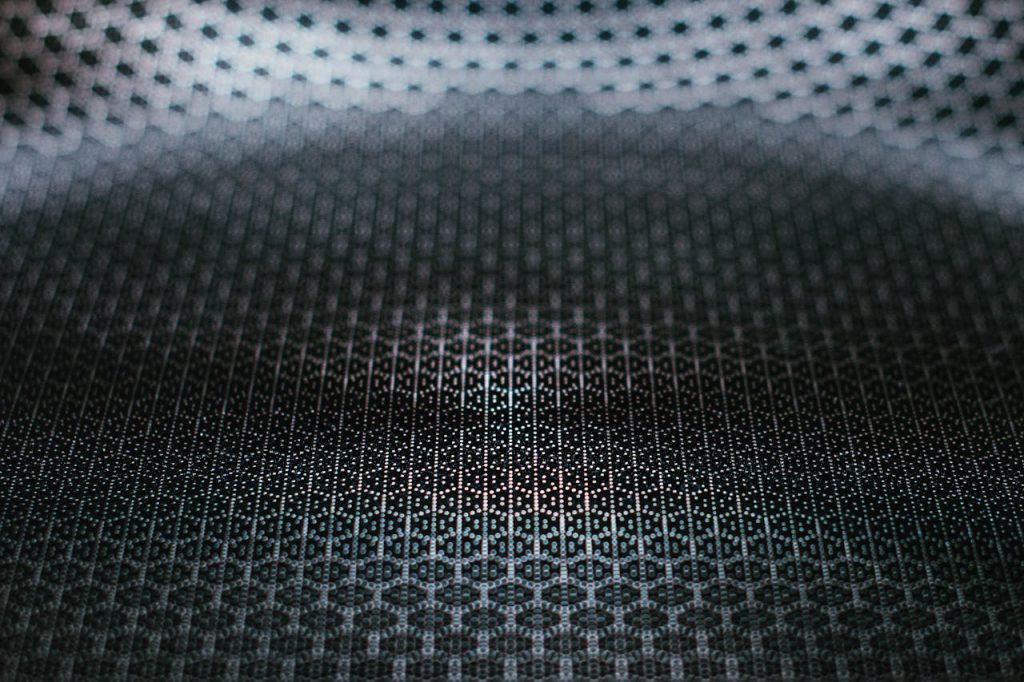

Alloy steel
Alloy steels, containing additional alloying elements, provide enhanced properties such as strength, hardness, and corrosion resistance. Laser welding is well-suited for these materials.
4140, 4340
These are chromium-molybdenum alloy steels known for their toughness and strength. Laser welding provides precise control over the weld pool, ensuring strong joints without compromising the material’s mechanical properties
8620
This low-alloy steel is commonly used in carburizing applications. Laser welding ensures strong, precise welds while maintaining the material’s core properties.
4130
Widely used in aerospace and automotive applications, 4130 alloy steel benefits from laser welding’s precision, which minimizes the risk of thermal cracking and distortion.
Stainless steel
Stainless steel is commonly welded using laser technology due to its excellent corrosion resistance and weldability.
Austenitic Stainless Steels (304, 316, and 321)
304 and 316: These austenitic stainless steels are renowned for their corrosion resistance. Laser welding offers excellent control over the weld pool, resulting in clean, high-strength joints. The low carbon content of 316 makes it particularly suitable for applications where corrosion resistance is critical, such as in marine and chemical environments.
321: This grade contains titanium, which enhances resistance to intergranular corrosion. Laser welding preserves these properties by minimizing heat input, ensuring the material’s structural integrity.
Martensitic Stainless Steels (410 and 420)
These martensitic stainless steels are known for their hardness and wear resistance. Laser welding is used to achieve precise control over the cooling rate, preventing cracking and ensuring strong, durable joints.
Ferritic Stainless Steels (430 and 446)
430: A ferritic stainless steel that benefits from laser welding due to its ability to produce high-quality welds without the need for post-weld annealing. This grade is often used in automotive trim and appliances.
446: This ferritic stainless steel is highly resistant to oxidation and scaling at high temperatures. Laser welding maintains these properties by controlling the heat input, making it suitable for applications in high-temperature environments such as industrial furnaces.
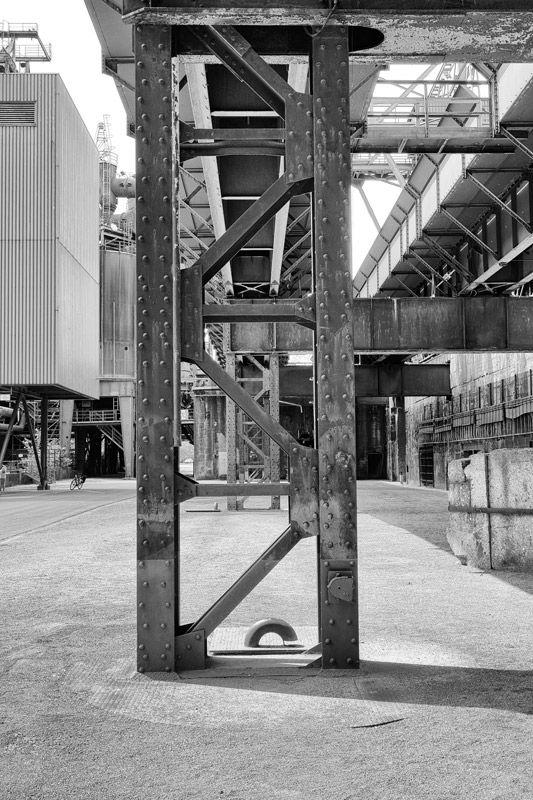
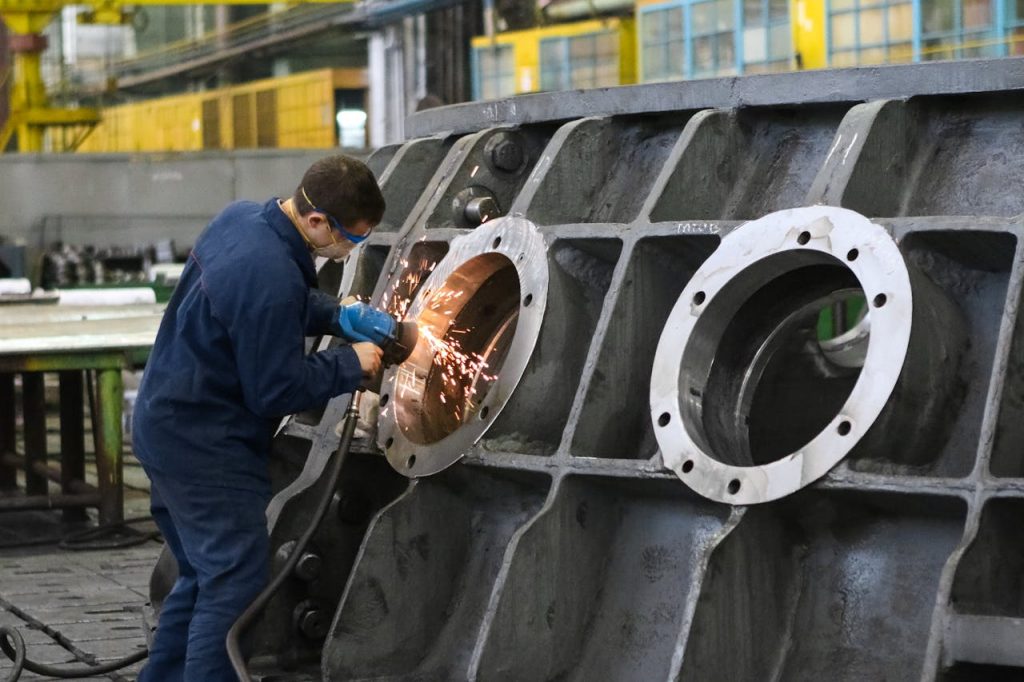
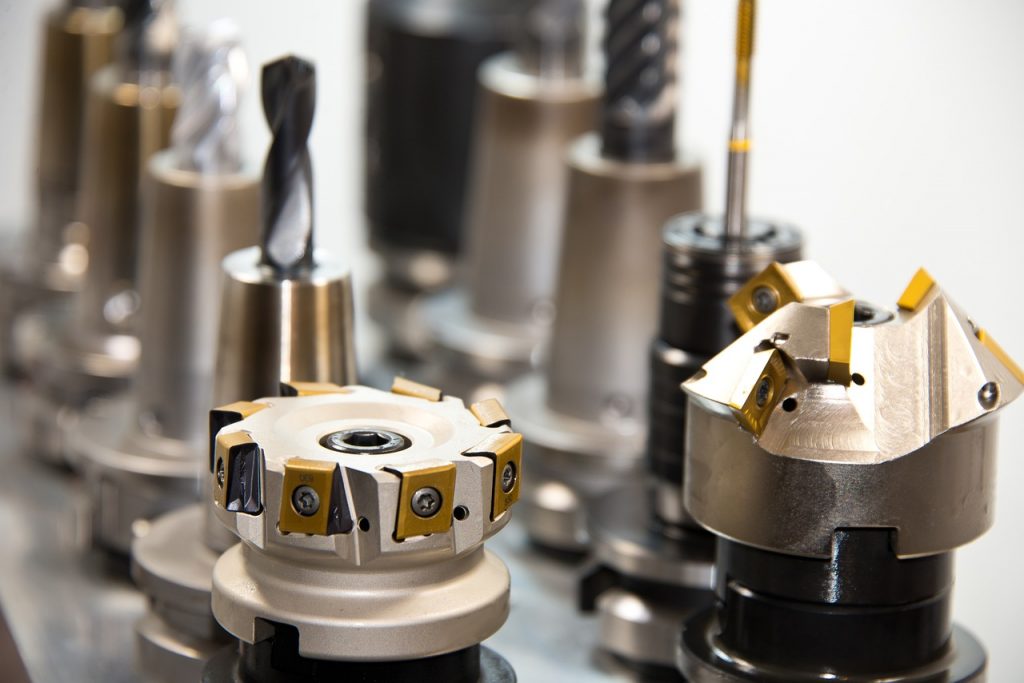
Tool and Die Steels
Tool and die steels are crucial in manufacturing for creating molds and dies. Laser welding is particularly beneficial for repairing and joining these materials, providing precise control to prevent distortion and maintain hardness.
Tool Steels for Molds and Dies (S136, SKD-11, NAK80, P20)
S136, SKD-11, NAK80: These tool steels are widely used in molds and dies due to their hardness and durability. Laser welding is commonly employed to repair surface defects and join components without compromising the material’s mechanical properties.
P20: Often used in plastic mold tooling, P20 benefits from the precision of laser welding, which minimizes the risk of thermal cracking and helps maintain the material’s toughness.
Hot-Work Tool Steels (8407, 718, 738, H13)
8407, 718, 738: These hot-work tool steels require careful welding techniques to minimize thermal stress and maintain their high-temperature strength. Laser welding offers the precision needed to manage these challenges, ensuring the integrity of the weld.
Proper control of thermal cycles during welding is crucial to avoid detrimental effects on the heat-affected zone (HAZ), such as excessive hardness or potential cracking.
H13: Known for its toughness and resistance to thermal fatigue, H13 can be effectively laser welded to ensure strong, durable joints. However, due to its high hardenability, careful management of thermal cycles during laser welding is essential. This helps to prevent excessive hardness in the HAZ, which can lead to brittleness and increase the risk of cracking.
Post-weld heat treatment is also recommended to temper the steel, improving the overall toughness and performance of the weld, particularly in demanding applications such as die casting and extrusion.
High-Alloy and Wear-Resistant Tool Steels (W302, 2344)
These high-alloy tool steels are valued for their exceptional wear resistance. Laser welding is used to control the heat-affected zone, preserving their wear-resistant properties and ensuring strong, durable welds.
Aluminium
Aluminum presents unique challenges for welding due to its high thermal conductivity and reflectivity. However, with the use of lasers and appropriate filler materials, aluminum alloys can be successfully welded while mitigating issues such as hot cracking and the formation of brittle phases.
6061
Widely used in aerospace and automotive applications, 6061 aluminum alloy benefits from laser welding’s ability to control heat input and avoid defects such as porosity and cracking. The precision of laser welding ensures strong joints without compromising the material’s structural integrity. Selecting the right filler material is also crucial to match the alloy’s properties and prevent defects.
7075
Known for its high strength, 7075 aluminum alloy is commonly used in aerospace applications. However, welding 7075 is challenging due to its susceptibility to hot cracking and the formation of brittle phases. Laser welding provides the precision needed to join this material without introducing defects, but it is essential to use appropriate filler materials to ensure a strong, reliable joint suitable for high-stress environments.
2024
This high-strength aluminum alloy is used in aerospace and military applications. Laser welding ensures strong joints while minimizing distortion and maintaining the material’s mechanical properties. As with other high-strength aluminum alloys, the choice of filler material plays a key role in preventing hot cracking and ensuring the longevity of the weld.
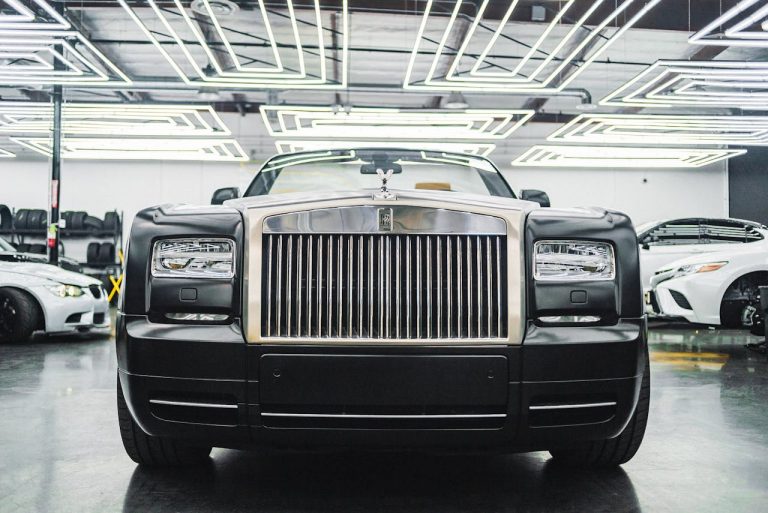
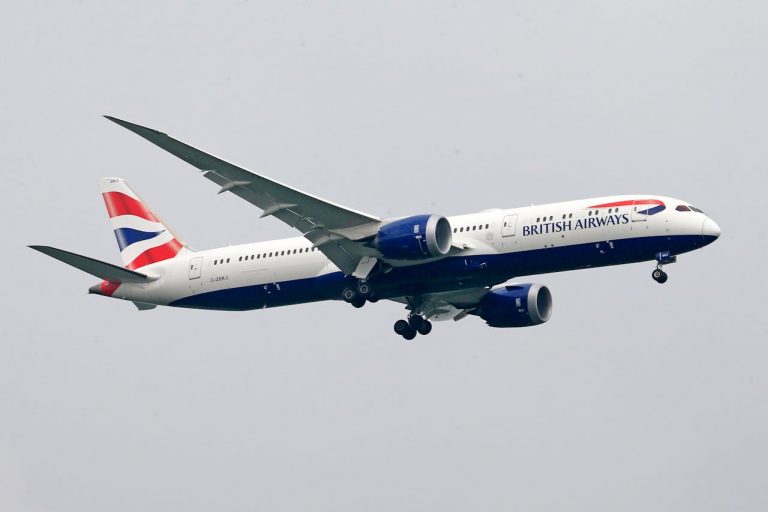

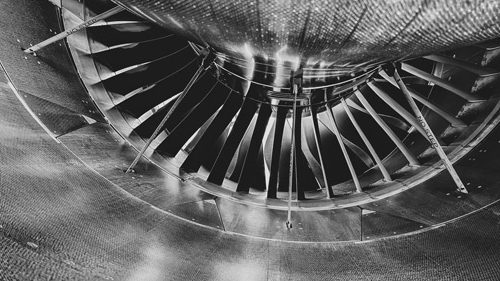
Titanium
Titanium and its alloys are highly valued for their strength, corrosion resistance, and biocompatibility. Laser welding is particularly suited for these materials due to its ability to produce high-quality welds with minimal contamination. To achieve optimal results, it is crucial to use an inert gas environment, typically argon, to shield the weld area from atmospheric contamination, which can severely compromise the weld’s quality.
Ti-6Al-4V
This titanium alloy is extensively used in aerospace, medical, and industrial applications. Laser welding ensures minimal contamination and high joint integrity, both of which are critical for these high-performance applications. The use of an inert gas shield, such as argon, is essential to protect the weld pool from oxygen, nitrogen, and hydrogen, which can lead to embrittlement and other weld defects.
Grade 2 Titanium
Known for its excellent corrosion resistance and formability, Grade 2 titanium is commonly used in chemical processing and marine applications. Laser welding provides precise control over the weld pool, resulting in clean, strong joints. An inert gas environment is vital during welding to maintain the alloy’s corrosion resistance and prevent contamination, which could degrade the material’s performance.
Grade 5 Titanium (Ti-6Al-4V)
This is the most commonly used titanium alloy, recognized for its high strength and corrosion resistance. Laser welding is ideal for applications requiring high-quality, contamination-free welds. Ensuring an inert gas shield, typically argon, is crucial during the welding process to avoid atmospheric contamination and to preserve the alloy’s desirable properties.